從流程管理層面推進精益管理
日期:2016-10-21 / 人氣: / 來源:www.bjjianyan.cn / 熱門標簽:
l 消除浪費
生產活動過程中不直接創造價值的活動全部可以定義為浪費,精益變革活動推進是從消除浪費角度切入,加強增值部分在整個運營中占比的過程。根據有關資料的調查,一般認為一家企業運營過程中95%以上的活動都是浪費。如下圖,若我們把改善切入點放在怎樣提升增值占比時,就算改善輔導達到100%,其整體的效果來講,增值部分在整個運營中的占比只有10%。若反過來,我們把切入點放在消除浪費上,我們就會發現,就算改善幅度只有50%,其改善成果來看時,增值部分在整個運營中的占比就52.5%。
浪費的區分方法中最為常見也是最普遍的是以浪費的形態劃分的豐田7大浪費,也就是等待的浪費、加工本身的浪費、動作浪費、庫存浪費、制造不良的浪費、生產過剩的浪費、搬運的浪費。
l 建立流動運營系統
“戶樞不蠹、流水不腐”,創造價值的各個步驟必須要全面流動起來,停滯就是一種浪費的表現。停滯代表的是現場的庫存、現場的不良品、未發貨的成品、等待使用的原材料等等,這種停滯物品的多少直接與產品的交付周期長短有關聯、直接與企業的現金流管理有關聯。
影響企業運營發生停滯的主要原因有生產批量的大小和運營過程中存在的瓶頸。那么讓系統流動起來,也就是發現瓶頸、消除瓶頸并把生產批量不斷縮小,直至實現單件流的過程。如下圖所示,水流足夠大時我們是無法看到水底下的暗礁隱患,這種隱患我們雖然看不到,但他們是確確實實存在的,也是在影響著整個水流的流動速度和流動量的。這與企業運營基本一致,當生產批量較大時,企業內部運營過程中發生的設備故障、物料損耗、產品不良、返工以及生產周期時間過長等問題都是無法感知到的,因為雖然生產成本居高不下,但很多情況下以大量的庫存的制造成本為代價,還是可以按時出貨、滿足客戶的需求的。
解決這種逆境的方法中最有效的方法之一,就是不斷的降低水面,讓水下的暗礁一點一點的顯露出來,而我們呢,發現一個暗礁,就處理一個,然后繼續降低水面,直到看不到一丁點暗礁為止。把上述方法應用在生產過程中,那就是不斷減少生產批量,達到均衡化生產的目的。為了達到這種變革目的持續要改進如快速換模、不良率降低、標準化工作推進以生產效率提升等一系列工作。在這種操作模式下,如果準備工作不充分,很容易發生在變革初期相應的現場管理指標變差的現象,在這種情況下我們管理團隊必須要正視這種問題的同時,也要從管理角度上設置其他精益管理指標進行管控,因為精益變革初期雖然一些傳統指標變差了,但更為積極的是肯定有很多精益指標變好了,如在制品庫存的金額、產品交貨周期、庫存周轉率、快速響應速度等等。
l 按需求拉動,避免過量生產,實現準時化生產(JIT)
推動式生產模式可以說是傳統生產系統下造成大量庫存和浪費的主要原因。精益變革過程中,按需求拉動式生產是實現準時化生產(JIT)的技術承載。
需求拉動式生產方式是在儲備一定的成品和工序在制品的條件下,根據需求由后向前層層拉動每道工序生產,從而達到按時按量提供所需產品。通過需求拉動式生產來促進企業各個環節不斷改善從而達到精益生產的目標,是企業實施精益生產的必經之路。
需求拉動式生產以準時化生產為核心,以降低成本、持續改善和提高為目標,通過需求拉動式組織方式的實現來逐步消除無效生產,壓縮庫存儲備,降低生產成本,更加及時和有效地滿足市場需求的變化,不斷改進和完善系統運行方式,從而逐步達到精益生產的要求。
準時化生產指的是在正確的時間、以正確的方式、按正確的路線,把正確的物料,送到正確的地點、每次都剛好及時。
需求拉動式生產方式是立足于企業的實際,在質量控制達標是3西格瑪標準的情況下,推進初期允許設立有少量安全的庫存和在制品儲備。實現拉動生產模式最有效的方法之一是應用KANBAN系統。通過KANBAN的傳遞,替代原有計劃模式下的排產計劃,實現拉動式生產。有3種不同的拉動生產系統模式,其一是補充式拉動系統、其二是順序式拉動系統。
l 不斷設定標準并改進標準
設定標準的最主要目的是減少變異或流程的波動。無論我們采用了KANBAN拉動生產模式也好,流動生產系統也好,如果沒有明確的標準其落實效果肯定不能達到導入這種精益系統的預期。在精益變革過程中我們要持續進行否定現在的流程、改善程更為優秀的流程、針對改善成果設定標準、按照標準進行操作的循環工作。
在精益變革中我們要設定很多標準,其中最為重要的是標準作業。標準作業是針對以人的動作為中心的重復性工作設定的標準,它包括T.T、作業順序、標準在庫。標準作業中設定是以現場員工的實際參與為基礎,明確規定了工位描述、動作步驟、圖示圖片、物料描述、工具描述、審批更改、安全要點、質量檢查、關鍵質量、時間要素。
在實際變革過程中很多推進人員最為頭疼的事情之一是改善成果不能維持,其主要的原因是,所制定的操作方法或改善手法,現場操作工沒有完全按照標準執行下去。標準和實際操作差異越大,改善難度就越高。在精益變革初期,我們必須要花很多時間對現有的工作進行標準化,并定期進行現場審核,保證標準化執行率逐步提升。在這個階段無論標準化的內容是否恰當,我們都應該把重點放在他們執行的一致性上。為了實現這點,在推進標準化初期,一定是以現場員工或班組長為中心推進標準化工作。
l 自主管理、追求零缺陷 (自働化)
精益變革中我們不斷最尋的是動態平衡,是速度和質量的平衡。就像下圖中所展現,精益生產的2大支柱是JIT和自働化。為了實現準時化生產,在生產運營各個環節我們所采取的措施都是怎樣提升速度及效率;同理為了實現自働化我們要通過自主管理、停線機制、安燈、簡易自動化等措施保證產品的質量。
一般來說,自主管理是主要通過員工的自我約束,自我控制,自我發現問題,自我分析問題,自我解決問題,以變被動管理為主動管理,進而自我提高,自我創新,自我超越,推動組織不斷發展與前進的管理方式。精益變革中指的自主管理與上述內容相比應該說更為狹隘,主要指的是質量管理領域上的自主性,具體指的是自己主動檢查所生產工序之品質、自己主動檢查負責工序來料之品質、自己主動檢查所負責工序設備狀況。
停線機制是為了防止不良品流入到后工序,在生產活動過程中發現不良品時有一線員工主導決定停線,并促使相關人員改進的一種管理手法。為了更好的實現停線機制現場經常應用的是安燈設備,它可以起到以可視化的方式第一時間把現場問題通報給相關人員的作用。停線機制很簡單,但真正實施到位的企業不多,最重要的原因是沒有做好可真正實施停線機制必須的工作。推進停線機制時必須要做好以下幾點工作
1) 明確過程質量控制基準,要做到生產系統和質量系統人員的標準的一致性;
2) 分層管理基準明確。根據問題的類型和復雜度,設定不同層級的人員對應;
3) 現場問題解決臺賬管理。當現場發生問題時,發生最多的是現場來了很多人,但沒有辦法解決現場問題或沒有人愿意拍板確定措施。如果一線班組長、工藝工程師、品質工程師等不同層級人員,根據以往處理問題的數據整理了一份解決問題臺賬,那么上述問題就可以迎刃而解。
4) 停線點設計和緩沖區設計等
停線機制的運營直接與當前生產任務的達成相關,這也是停線機制很難落實下去的原因。雖然長遠來看,停線機制肯定對企業發展有利,但短期來看也確實是影響每日的生產。那么在推進停線機制過程中我們也要重點考慮怎樣降低他對生產的影響。普遍采用的方式是在生產工藝流程中,根據CTQ(關鍵質量特性)工位、特殊工位以安全法規工位等重點工位為主設定停線點,并在每個停線點設定一定數量的緩沖庫存量,以此來確保對生產的直接影響。這種緩沖庫存的設計是占時的,我們可以根據精益變革的進程,逐步減少緩沖庫存量,以此達到持續變革的最終目的。
局部的最佳,不代表整體效果最優化。精益變革過程中我們一定要以客戶的需求為導向,以宏觀角度發現問題、改善問題,力求全流程整體的最優化。
如下圖所示,在產品研發過程中每個研發小組站在部門的角度所設計的產品都最優秀的,但等到把4個組開發出來的產品組合在一起時,我們發現他與客戶的期望相差甚遠。
生產活動過程中不直接創造價值的活動全部可以定義為浪費,精益變革活動推進是從消除浪費角度切入,加強增值部分在整個運營中占比的過程。根據有關資料的調查,一般認為一家企業運營過程中95%以上的活動都是浪費。如下圖,若我們把改善切入點放在怎樣提升增值占比時,就算改善輔導達到100%,其整體的效果來講,增值部分在整個運營中的占比只有10%。若反過來,我們把切入點放在消除浪費上,我們就會發現,就算改善幅度只有50%,其改善成果來看時,增值部分在整個運營中的占比就52.5%。
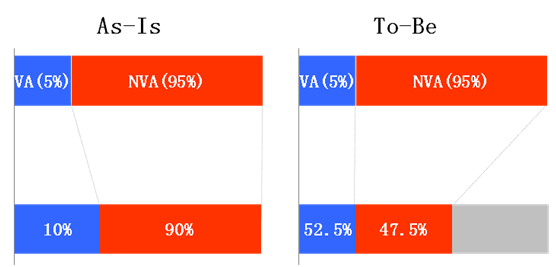
消除浪費有效性示意圖
浪費的區分方法中最為常見也是最普遍的是以浪費的形態劃分的豐田7大浪費,也就是等待的浪費、加工本身的浪費、動作浪費、庫存浪費、制造不良的浪費、生產過剩的浪費、搬運的浪費。
l 建立流動運營系統
“戶樞不蠹、流水不腐”,創造價值的各個步驟必須要全面流動起來,停滯就是一種浪費的表現。停滯代表的是現場的庫存、現場的不良品、未發貨的成品、等待使用的原材料等等,這種停滯物品的多少直接與產品的交付周期長短有關聯、直接與企業的現金流管理有關聯。
影響企業運營發生停滯的主要原因有生產批量的大小和運營過程中存在的瓶頸。那么讓系統流動起來,也就是發現瓶頸、消除瓶頸并把生產批量不斷縮小,直至實現單件流的過程。如下圖所示,水流足夠大時我們是無法看到水底下的暗礁隱患,這種隱患我們雖然看不到,但他們是確確實實存在的,也是在影響著整個水流的流動速度和流動量的。這與企業運營基本一致,當生產批量較大時,企業內部運營過程中發生的設備故障、物料損耗、產品不良、返工以及生產周期時間過長等問題都是無法感知到的,因為雖然生產成本居高不下,但很多情況下以大量的庫存的制造成本為代價,還是可以按時出貨、滿足客戶的需求的。
解決這種逆境的方法中最有效的方法之一,就是不斷的降低水面,讓水下的暗礁一點一點的顯露出來,而我們呢,發現一個暗礁,就處理一個,然后繼續降低水面,直到看不到一丁點暗礁為止。把上述方法應用在生產過程中,那就是不斷減少生產批量,達到均衡化生產的目的。為了達到這種變革目的持續要改進如快速換模、不良率降低、標準化工作推進以生產效率提升等一系列工作。在這種操作模式下,如果準備工作不充分,很容易發生在變革初期相應的現場管理指標變差的現象,在這種情況下我們管理團隊必須要正視這種問題的同時,也要從管理角度上設置其他精益管理指標進行管控,因為精益變革初期雖然一些傳統指標變差了,但更為積極的是肯定有很多精益指標變好了,如在制品庫存的金額、產品交貨周期、庫存周轉率、快速響應速度等等。
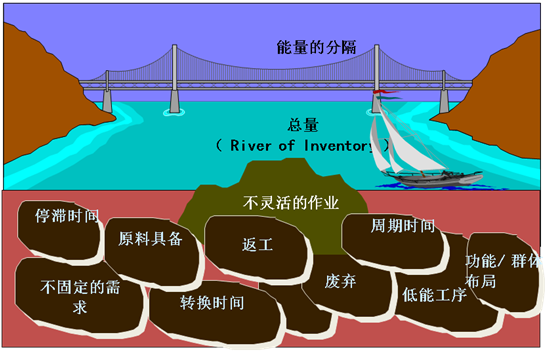
企業運營瓶頸圖示
l 按需求拉動,避免過量生產,實現準時化生產(JIT)
推動式生產模式可以說是傳統生產系統下造成大量庫存和浪費的主要原因。精益變革過程中,按需求拉動式生產是實現準時化生產(JIT)的技術承載。
需求拉動式生產方式是在儲備一定的成品和工序在制品的條件下,根據需求由后向前層層拉動每道工序生產,從而達到按時按量提供所需產品。通過需求拉動式生產來促進企業各個環節不斷改善從而達到精益生產的目標,是企業實施精益生產的必經之路。
需求拉動式生產以準時化生產為核心,以降低成本、持續改善和提高為目標,通過需求拉動式組織方式的實現來逐步消除無效生產,壓縮庫存儲備,降低生產成本,更加及時和有效地滿足市場需求的變化,不斷改進和完善系統運行方式,從而逐步達到精益生產的要求。
準時化生產指的是在正確的時間、以正確的方式、按正確的路線,把正確的物料,送到正確的地點、每次都剛好及時。
需求拉動式生產方式是立足于企業的實際,在質量控制達標是3西格瑪標準的情況下,推進初期允許設立有少量安全的庫存和在制品儲備。實現拉動生產模式最有效的方法之一是應用KANBAN系統。通過KANBAN的傳遞,替代原有計劃模式下的排產計劃,實現拉動式生產。有3種不同的拉動生產系統模式,其一是補充式拉動系統、其二是順序式拉動系統。
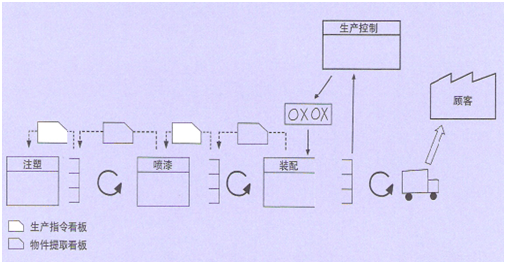
不充式拉動系統
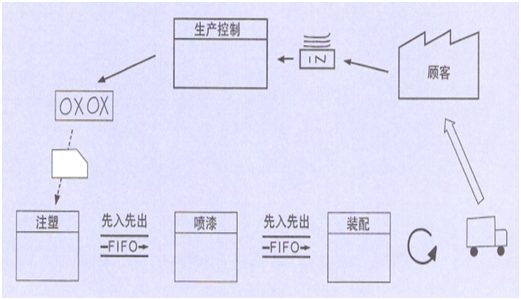
順序式拉動系統
l 不斷設定標準并改進標準
設定標準的最主要目的是減少變異或流程的波動。無論我們采用了KANBAN拉動生產模式也好,流動生產系統也好,如果沒有明確的標準其落實效果肯定不能達到導入這種精益系統的預期。在精益變革過程中我們要持續進行否定現在的流程、改善程更為優秀的流程、針對改善成果設定標準、按照標準進行操作的循環工作。
在精益變革中我們要設定很多標準,其中最為重要的是標準作業。標準作業是針對以人的動作為中心的重復性工作設定的標準,它包括T.T、作業順序、標準在庫。標準作業中設定是以現場員工的實際參與為基礎,明確規定了工位描述、動作步驟、圖示圖片、物料描述、工具描述、審批更改、安全要點、質量檢查、關鍵質量、時間要素。
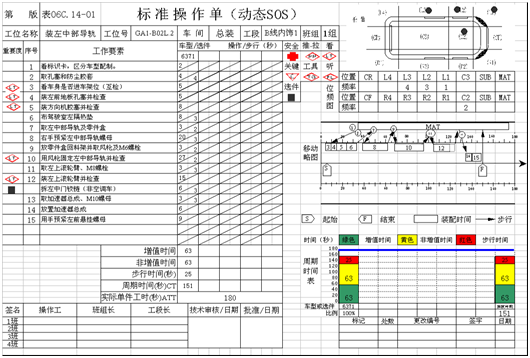
標準作業模板
在實際變革過程中很多推進人員最為頭疼的事情之一是改善成果不能維持,其主要的原因是,所制定的操作方法或改善手法,現場操作工沒有完全按照標準執行下去。標準和實際操作差異越大,改善難度就越高。在精益變革初期,我們必須要花很多時間對現有的工作進行標準化,并定期進行現場審核,保證標準化執行率逐步提升。在這個階段無論標準化的內容是否恰當,我們都應該把重點放在他們執行的一致性上。為了實現這點,在推進標準化初期,一定是以現場員工或班組長為中心推進標準化工作。
l 自主管理、追求零缺陷 (自働化)
精益變革中我們不斷最尋的是動態平衡,是速度和質量的平衡。就像下圖中所展現,精益生產的2大支柱是JIT和自働化。為了實現準時化生產,在生產運營各個環節我們所采取的措施都是怎樣提升速度及效率;同理為了實現自働化我們要通過自主管理、停線機制、安燈、簡易自動化等措施保證產品的質量。
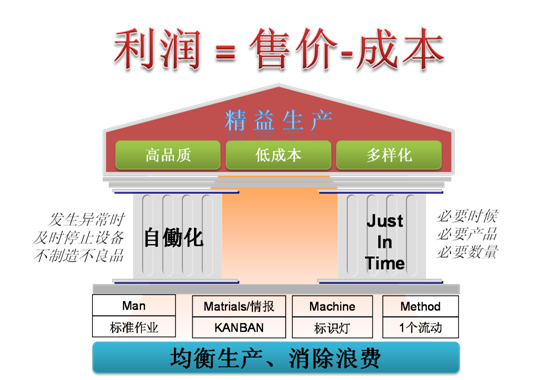
精益生產屋
一般來說,自主管理是主要通過員工的自我約束,自我控制,自我發現問題,自我分析問題,自我解決問題,以變被動管理為主動管理,進而自我提高,自我創新,自我超越,推動組織不斷發展與前進的管理方式。精益變革中指的自主管理與上述內容相比應該說更為狹隘,主要指的是質量管理領域上的自主性,具體指的是自己主動檢查所生產工序之品質、自己主動檢查負責工序來料之品質、自己主動檢查所負責工序設備狀況。
停線機制是為了防止不良品流入到后工序,在生產活動過程中發現不良品時有一線員工主導決定停線,并促使相關人員改進的一種管理手法。為了更好的實現停線機制現場經常應用的是安燈設備,它可以起到以可視化的方式第一時間把現場問題通報給相關人員的作用。停線機制很簡單,但真正實施到位的企業不多,最重要的原因是沒有做好可真正實施停線機制必須的工作。推進停線機制時必須要做好以下幾點工作
1) 明確過程質量控制基準,要做到生產系統和質量系統人員的標準的一致性;
2) 分層管理基準明確。根據問題的類型和復雜度,設定不同層級的人員對應;
3) 現場問題解決臺賬管理。當現場發生問題時,發生最多的是現場來了很多人,但沒有辦法解決現場問題或沒有人愿意拍板確定措施。如果一線班組長、工藝工程師、品質工程師等不同層級人員,根據以往處理問題的數據整理了一份解決問題臺賬,那么上述問題就可以迎刃而解。
4) 停線點設計和緩沖區設計等
停線機制的運營直接與當前生產任務的達成相關,這也是停線機制很難落實下去的原因。雖然長遠來看,停線機制肯定對企業發展有利,但短期來看也確實是影響每日的生產。那么在推進停線機制過程中我們也要重點考慮怎樣降低他對生產的影響。普遍采用的方式是在生產工藝流程中,根據CTQ(關鍵質量特性)工位、特殊工位以安全法規工位等重點工位為主設定停線點,并在每個停線點設定一定數量的緩沖庫存量,以此來確保對生產的直接影響。這種緩沖庫存的設計是占時的,我們可以根據精益變革的進程,逐步減少緩沖庫存量,以此達到持續變革的最終目的。
l 全流程整體優化
局部的最佳,不代表整體效果最優化。精益變革過程中我們一定要以客戶的需求為導向,以宏觀角度發現問題、改善問題,力求全流程整體的最優化。
如下圖所示,在產品研發過程中每個研發小組站在部門的角度所設計的產品都最優秀的,但等到把4個組開發出來的產品組合在一起時,我們發現他與客戶的期望相差甚遠。
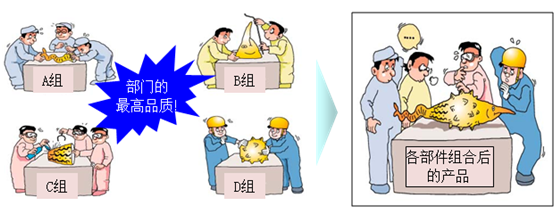
局部最佳和整體優化
作者:博革咨詢